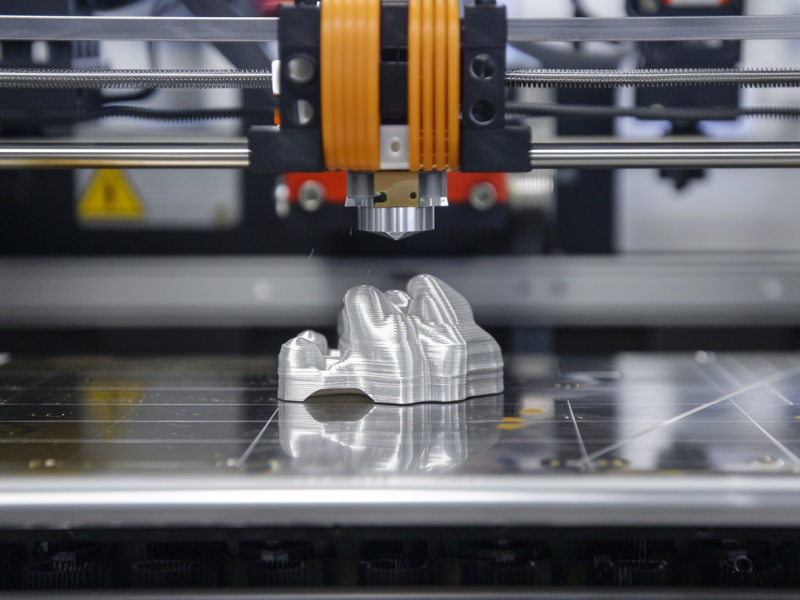
Introduction
Scandium is becoming an important material in 3D printing, particularly in additive manufacturing. Additive manufacturing builds objects layer by layer using materials like metal powders. Scandium, when combined with aluminum, creates an alloy that is strong, lightweight, and ideal for high-performance parts. This alloy is now widely used in industries such as aerospace, automotive, and medical. Let’s take a closer look at how scandium is improving 3D printing.
Scandium and 3D Printing of Metal Parts
In 3D printing, the choice of material makes a big difference. Metal powders used in additive manufacturing must be strong, resistant to corrosion, and easy to work with. Scandium-aluminum alloy powders meet these requirements. They are great for producing parts that need both strength and low weight. These qualities make them a top choice for industries that depend on high-performance components.
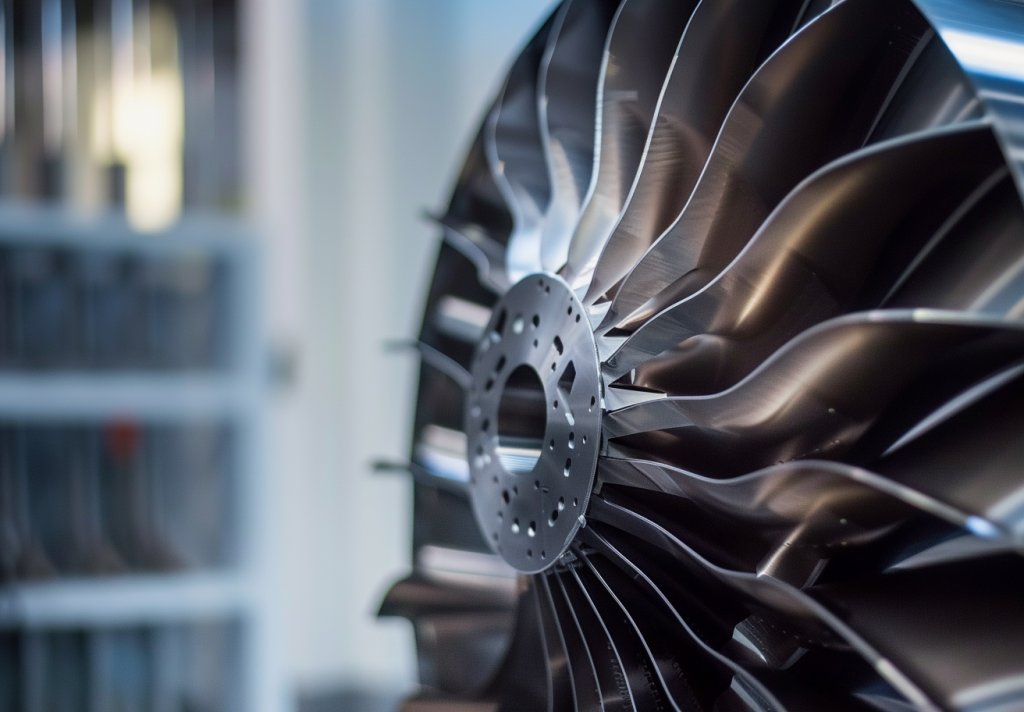
Scandium alloys help 3D printing create complex metal parts with less waste compared to traditional methods. Traditional manufacturing often involves cutting away excess material, which can be inefficient. 3D printing with scandium alloys uses only the amount of material needed, layer by layer. This also allows manufacturers to produce smoother surfaces and stronger joints in a single process.
Benefits of Scandium Alloys in High-Performance Parts
Scandium-aluminum alloys have several advantages when it comes to creating high-performance parts. First, they offer increased strength. Even a small amount of scandium can significantly improve aluminum’s strength without making it heavier. This is especially valuable in industries like aerospace and automotive, where weight and strength are both critical.
Scandium alloys also improve corrosion resistance. Aluminum, by itself, can corrode when exposed to harsh environments. However, adding scandium helps form a protective layer on the surface that prevents corrosion. This makes scandium-aluminum parts last longer and performs better in tough conditions.
Another benefit is that scandium alloys are highly flexible in design. 3D printing with scandium-aluminum allows engineers to create complex shapes and detailed parts that are difficult to make using traditional manufacturing methods. In aerospace, for example, this flexibility is essential for designing precise components that need to meet strict performance standards.
Examples of Scandium in Aerospace, Automotive, and Medical Industries
In the aerospace industry, scandium is playing an increasing role in reducing the weight of aircraft. Aircraft manufacturers are always looking for ways to make planes lighter while maintaining strength. Scandium-aluminum alloys help reduce the weight of critical parts, such as wing sections and engine components, without sacrificing safety. These lightweight parts lead to improved fuel efficiency, which is a major goal for airlines.
In the automotive industry, scandium is being used to create lighter, stronger parts. Car manufacturers are using scandium-aluminum alloys in engine components and suspension parts. These materials not only help improve fuel efficiency but also make vehicles more durable. For example, cars built with scandium-aluminum components can better withstand the wear and tear of daily use, which can extend the vehicle’s lifespan.
In the medical field, scandium alloys are being used to produce custom implants and prosthetics. Medical devices need to be both strong and lightweight, especially for patients who depend on them for mobility. Scandium-aluminum alloys meet these needs because they are light, resistant to corrosion, and compatible with the human body. Doctors can now use 3D printing to create custom implants that fit perfectly, improving patient comfort and reducing recovery time.
Recent Developments in Scandium 3D Printing
In recent years, scandium has become more accessible for 3D printing. In the past, the high cost of scandium limited its use. However, advancements in the extraction process have made scandium more affordable. This has opened the door for more industries to adopt scandium-aluminum alloys in their 3D printing projects.
Another important development is hybrid manufacturing. This method combines 3D printing with traditional manufacturing techniques. Scandium-aluminum alloys work well in this process. Manufacturers can use 3D printing to create complex parts and then finish them using conventional methods, reducing production time and cost while still benefiting from the advantages of 3D printing.
There is also ongoing research into improving scandium-aluminum alloys for 3D printing. Scientists are working on ways to make these alloys even stronger and more flexible. This could lead to new uses in sectors like defense and energy, where materials need to perform well under extreme conditions.
Conclusion
Scandium is becoming an essential material in 3D printing, particularly in the production of high-performance metal parts. Its ability to enhance the strength, corrosion resistance, and flexibility of aluminum makes it a valuable asset for industries like aerospace, automotive, and medical. Scandium-aluminum alloys allow manufacturers to create complex parts that are lighter, stronger, and more durable than those made with traditional materials. With recent advancements making scandium more affordable and easier to use, its role in 3D printing technologies will likely continue to grow.
If you’re interested in learning more about scandium alloys or how they can benefit your projects, contact Stanford Advanced Materials for more information.