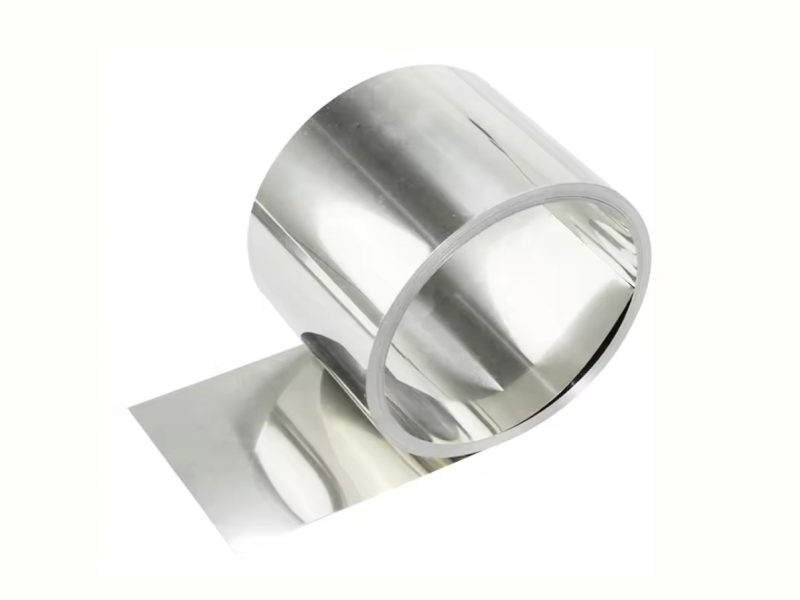
Introduction
In the realm of advanced materials, scandium stands out for its impressive array of properties that make it a sought-after element in various high-tech applications. Among its many forms, scandium foil represents a versatile material that embodies the element’s unique characteristics, offering strength, a lighter weight, and a high melting point. However, not all scandium foils are created equal; their thickness plays a pivotal role in determining their suitability for different applications. From the ultra-thin layers used in cutting-edge electronics and scientific research to the thicker variants essential for industrial processes, the thickness of scandium foil shapes its utility across a wide spectrum of technological and scientific endeavors.
This article delves into the significance of scandium foil thickness, exploring how it influences the material’s applications and underscores the importance of customization to meet specific needs. Whether it’s enabling breakthroughs in research or enhancing the efficiency of industrial processes, scandium foil’s versatility is a testament to its adaptability across diverse fields. As we navigate through the intricacies of scandium foil and its applications, we’ll see how thin truly matters in making the most of this remarkable material.
Read more: Scandium Introduction: Structure, Classification, and Characteristics
The Science of Scandium Foil
Scandium foil, a marvel of modern materials science, is a testament to the element’s utility beyond its modest presence on the periodic table. This thin material, crafted from scandium metal, combines several of the element’s hallmark properties: a lightweight nature, significant strength, and a high melting point, among others. The process of making scandium foil involves meticulous refinement and rolling techniques, which transform scandium from its raw, ore-derived form into thin, usable sheets.
What is Scandium Foil?
Scandium foil refers to scandium metal that has been processed and rolled into thin sheets. These sheets can vary greatly in thickness, catering to a wide array of applications. The adaptability of scandium foil, able to be as thin as a few micrometers or as thick as several millimeters, showcases its versatility.
Production Process
The journey from scandium ore to scandium foil is a complex one, involving several stages of extraction, purification, and physical transformation. Initially, scandium is extracted from its ores or recovered as a byproduct of uranium processing. Through a series of chemical reactions, pure scandium is isolated and then melted. Once in molten form, scandium is cast into ingots, which are then subjected to a series of hot and cold rolling processes to achieve the desired foil thickness.
Properties and Desirability
The allure of scandium foil lies in its combination of light weight, strength, and resistance to corrosion, making it an invaluable material in fields demanding such properties. Its high melting point ensures stability under extreme conditions, while its ability to alloy with other metals can significantly enhance the material characteristics of the resulting compound. For instance, scandium-aluminum alloys are renowned for their increased strength and reduced weight, a boon for aerospace and automotive applications.
Ultra-Thin Scandium Foils
Definition and Production Process
Ultra-thin scandium foils are high-purity scandium sheets with thicknesses often less than a few micrometers. Their production involves advanced rolling and annealing processes under controlled environments to achieve the desired thinness without compromising the metal’s integrity. Precision in manufacturing is crucial to maintain uniform thickness and surface smoothness.
Applications
These foils find applications in sectors demanding exacting standards:
- Electronics: In components where excellent conductivity and minimal weight are critical.
- Research: As substrates in experimental physics and chemistry due to scandium’s reactive properties.
- Aerospace: For lightweight, high-strength structural elements, contributing to fuel efficiency and payload increase.
Case Studies
- In electronics, ultra-thin scandium foils have enabled the development of more efficient transistors, showcasing improved performance at reduced sizes.
- Aerospace examples include the use of scandium foils in experimental aircraft designs, where every gram of weight reduction can significantly impact performance and cost.
Thicker Scandium Foils
Characteristics and Manufacturing
Thicker scandium foils, while still relatively thin, are robust enough to be used in applications where durability and structural integrity are essential. Their production follows similar principles to the thinner foils but allows for a bit more flexibility in the rolling process to achieve greater thicknesses.
Applications
- Industrial Processes: As components in machinery where strength and resistance to heat are vital.
- Energy Solutions: In fuel cells and batteries for efficient conductivity and long-term stability.
- Structural Components: For advanced engineering projects requiring materials that offer a balance between strength and lightweight.
Examples
- Industrial machinery often incorporates thicker scandium foils in components exposed to high temperatures or corrosive substances.
- In energy, scandium foils are utilized to enhance the longevity and efficiency of next-generation batteries and fuel cells.
Customization for Specific Needs
Customizing Thickness
The customization of scandium foil thickness is essential for its application across industries. Manufacturers work closely with clients to determine the optimal thickness for their specific applications, balancing performance requirements with material costs.
Enhancing Utility
Customization allows for scandium foils to be tailored to specific technological and scientific endeavors, maximizing efficiency and effectiveness. Whether reducing weight in aerospace components or improving conductivity in electronic devices, customized thickness plays a critical role.
Conclusion
Scandium foil’s versatility, dictated by its thickness, underscores its growing importance in various applications. From ultra-thin layers enhancing electronics to thicker foils strengthening aerospace structures, the ability to customize thickness ensures scandium’s relevance in future technological advancements. The continued exploration and innovation in scandium foil manufacturing promise to expand its applications, driving progress in industries worldwide.
To inquire about high-quality scandium alloys, please contact us.