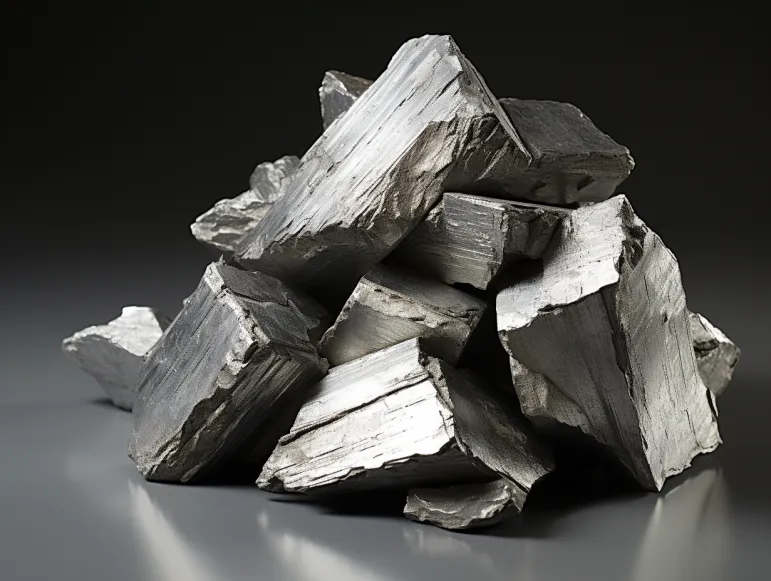
Adopted from Ashurst Technology Web Page
Scandium is one of the most potent alloying elements in the periodic table. When added to aluminum alloys, scandium can significantly increase strength and reduce grain size. Scandium has been added to aluminum alloys in the former soviet union for missiles and MIG fighter applications.
The following graph was reproduced from data given by various authors at the ” Scandium 94 Conference ” held in Moscow. As can be seen, the addition of Scandium increases the yield strength of many aluminum alloy systems.

Scandium achieves these improved properties in Al-Sc alloys through superior fundamental dispersoid characteristics:
- Highly Coherent Dispersoids
- Greater Volume Fraction of Dispersoids (more soluble and lower atomic wt.)
- Greater Thermal Stability
These characteristics achieve these performance improvements over conventional alloys:
- Improved Strength
- Improved Resistance to Recrystallization
- Reduced Grain Size
- Improved Resistance to Hot Cracking
Scandium provides the highest increment of strengthening per atomic percent of any alloying element when added to aluminum.
Click here to find out a list of of Al-Sc related papers collected by Mr. Jostein Røyset at the Norwegian University of Science and Technology, Department of Metallurgy.
Highly Coherent Dispersoids
The Al3Sc dispersoid is an L12-type phase which is coherent with the aluminum matrix. An extremely high coherency mismatch is observed for the Al3Sc phase resulting in significant lattice strain to block dislocation motion and to impede grain growth. This mismatch is 1.2% compared with 0.8% for Al3Zr, one of the next most potent dispersoids.

Greater Volume Fraction of Dispersoids
(more soluble and lower atomic weight.)
Compared with other grain refining elements used in aluminum alloys (e.g. Zr, Ti, Mn, Cr) a greater volume fraction of Sc can be added. As shown in the table below, this is especially evident when the volume atomic percent maximum solubility is considered.
A greater volume fraction effectiveness is important to inhibit recrystallization and prevent subgrain annihilation and coalescence. The high coherency strain further impedes the motion of grain boundaries resulting in a finer grain structure and higher strength through the well-known Hall-Petch relationship.
Alloying Element | Solubility(Wt. %) | Solubility(Vol Atomic %) |
Sc | 0.50 | 0.30 |
Ti | 0.18 | 0.05 |
Zr | 0.15 | 0.08 |
Mn | 0.30 | 0.15 |
Cr | 0.25 | 0.13 |
V | 0.10 | 0.05 |
Greater Thermal Stability
The Al-Sc phase diagram below shows the Al-Al3Sc eutectic reaction to take place at an unusually high temperature. This high solidification temperature improves the heterogeneous nucleation of grains, resulting in refined grain size (and reduced hot cracking). A reduction in hot cracking is especially important for the welding of high-strength alloys. Most of the highest-strength aluminum alloys are not weldable and the addition of Sc can improve the weldability of many of these alloys.
Perhaps a more important aspect of the greater thermal stability of the Al3Sc dispersoids is their effectiveness at reducing recrystallization. Heavily cold alloys (such as extruded and/or drawn bats, bike frames, and tubes) contain sufficient stored energy to cause recrystallization. This results in substantial strength loss. Designers know that thin-walled products have less strength than thicker sections due to this softening effect. The addition of Sc can eliminate this problem in many combinations of alloy, heat treatment, and mechanical working.
Microstructures can be viewed to see the remarkable reduction in recrystallization from the addition of Sc. The sample microstructures for extruded 7x7x series baseball bat materials are shown on a separate page. (Warning: To provide high-resolution microstructures, these GIF images are each about 150k in size.)
The following table shows the effective recrystallization temperature performance of different dispersoids:
Element | Recrystallization Temp. (C) |
Mn | 325 |
Cr | 325 |
Zr | 400 |
Sc | 600 |

I’m not sure where you’re getting your info, but good topic.